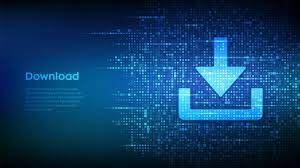
Time dependent properties first steps (SAP2000)īasic introduction to using time dependent material propertiesīasic introduction to hinge application in SAP2000. Procedure for modeling simply supported shells and coordinating their support systems.Ĭircular openings may be created within area objects, and the surrounding mesh may be improved.
#Changing names of frames sap 2000 manual#
This tutorial describes a manual modeling process for wall-type bents within bride objects. Setting the tolerance for cutting planes within 2D views such that all desired objects are displayed. Guidelines and tutorial for creating a steel-girder bridge with variable flange thickness. Steel-girder bridge with variable flange thickness Procedure for developing a model with variable girder spacing. Tutorial included with the SAP2000 Bridge Examples document. Model from the SAP2000 Bridge Examples document. Tutorial included in the SAP2000 bridge-examples document. Procedure for initiating step-by-step moving-load analysis. Step-by-step moving-load analysis first steps (SAP2000) Procedure for initiating influence-based moving-load analysis. Influence-based moving-load analysis first steps (SAP2000) Materials, sections, grids, and supports are defined. Guidelines for the manual modification of bridge bearings automatically created by the bridge modeler.Ĭreate and modify a concrete bent which features a nonprismatic cap beam. Modify joints and apply constraints such that a pin connection allows crossing members to translate freely. Modeling a pin connection between crossing members
#Changing names of frames sap 2000 how to#
Options and an example of how to obtain results for individual stages of a staged-construction load case.Īn overview of the tuned-mass damper and guidelines for modeling the device.Ĭoncrete confinement for Caltrans sectionsĬhanging the confinement characteristics for reinforced-concrete Caltrans sections within the Section Designer. Obtain results for individual stages of a staged-construction load case Guidelines for creating complicated joint patterns using interactive database editing. Guidelines for defining vertical and horizontal layout lines, also known as baselines. Use the Section Designer to create a bulb-girder section with rounded corners.Ĭreate custom sections using polygonal shapesĬreate custom cross sections by drawing polygonal shapes within the section designer, then modify or add to their geometry through reshape mode or interactive database editing. This tutorial provides an introduction to the assignment of joint patterns.Ĭreate bulb-girder sections with rounded corners Guidelines and tutorial for modeling haunched steel-girder bridges. Several approaches to the modeling of composite sections.Ī detailed and extensive procedure which describes the modeling, analysis, and design of a 3D steel-frame pipe rack system. Introductory tutorial for using section cuts. Applicable to static, modal, and buckling load cases. Guidelines for acceleration-load application in an arbitrary direction. Guidelines for performing pushover analysis. Overview of the procedure for time-history analysis. Reinforced-concrete column and beam designĭesign reinforced-concrete columns and beams while considering combined performance measures and interaction-surface output. Steel used in all cases was A9950Įach Property was allotted to appropriate auto selection list of diverse sections so that Sap2000 designs them in accordance with that list.An overview of the design-check procedure for steel-frame structural systems. There were no selected templates in the beginning of the model, a grid model was arranged considering the small details of the frame with the purpose of drawing it without any difficulty.įollowing sections were allotted to equivalent members so as to design them individually. Detailed calculation are out of vision of this text and can be submitted on request. Load calculations are executed for dead, live, wind and roof cases. SAAP applies this list afterward to deliver initial design sections. AUTO list refers to a library of all the ASCE certified sections that is imported into SAAP. Analysis was run and then ASCE 7-10 is applied to design load combinations sections through sap auto list. Loads were initially supposed in accordance with ASCE 7-10 and then were dispersed on frame A-A. Just frame A-A was modeled to retain things uncomplicated and comparatively precise. Designed frame is ?pinned? and it signifies that it withstands lateral forces through a bracing system. The process for designing the steel frame in sap2000 is completed. Given below a sample of office building plan as well as the process of design :. Steel structures are mostly recognized in the construction industry because these are accessible simply and require fewer time in fabrication.
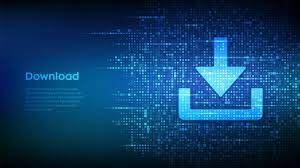